妥協のない効率化で
新時代の
自動車ガラスを。
自動車業界は今、100年に1度の大変革期を迎えている──このプロジェクトはその渦中で幕を開けた。全部門の関係者が集い行われた意見交換会の議題は、マツダ社が期待を込めて市場に投入する『CX-60』について。自動車用ガラス部品を設計する開発実研部の豊田が求められていたのは、製造工程の効率化だ。同じ頃ガラス組立課の栗原も同様に、質の高い製造工程の確立という課題を抱えていた。今回はこの二人の視点を通し『CX-60』のガラス部品開発秘話に迫る。
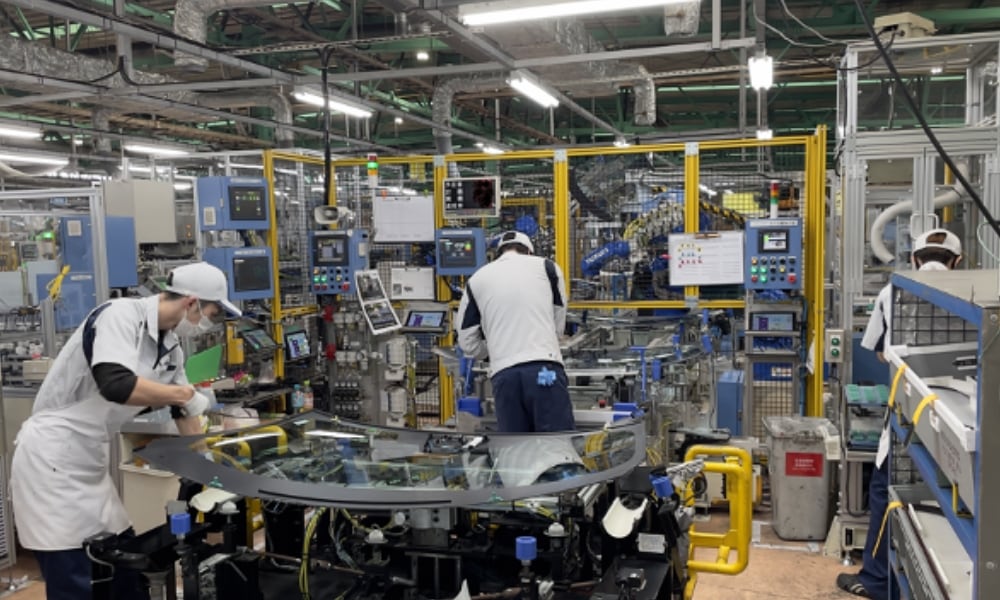
概要
内 容 | CX-60のガラス部品の開発 |
---|---|
期 間 | 2年間 |
従事社員数 | 30名以上 |
要求事項 | 製造工程の効率化・質の高い製造工程と管理の実施 |
樹脂形状に工夫を施し不具合をゼロに
自動車用ガラスの設計といってもその業務は多岐にわたる。設計主査として依頼元と工場をつなぐパイプ役も務めた豊田は現場担当者をはじめサプライヤーとも協議し、様々な視点から設計に取り組んだと語る。「今回からガラスに接着する樹脂部品の設計にも携わっています。以前は接着のために特別な治具(ジグ)が必要でしたが、樹脂部品の形状自体を最適化し、直接取り付けられるようにしたことで不要となりました」。この工夫は製品づくりの新たなノウハウとして『CX-60』以降の車種にも適用されている。「設計という自分たちの領域内で課題を解決できたことが嬉しかったですね。精度の高い製品づくりができることはやりがいの一つになっています」。
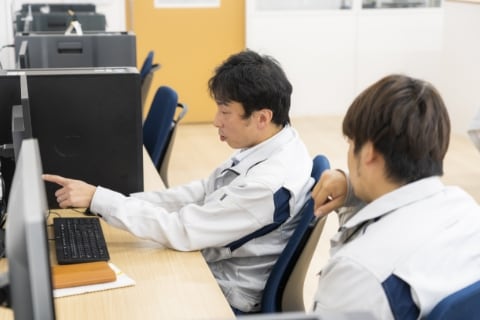
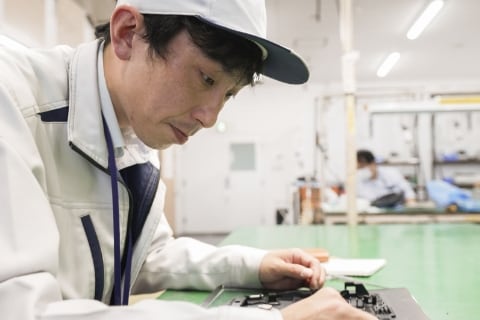
工程内不良を撲滅した製造ラインの自動化
設計によって改良された製品を安定して量産する工程設定、管理を担当するのが栗原の仕事だ。彼が今回力を入れて取り組んだのは製造工程の自動化だった。「品質を安定させるため設備を導入し、部品の搬送・接着剤塗布・ガラスへの貼り付けという一連の流れを自動化できるよう設定しました。設備製作にはかなりの時間を費やしましたが、これまで培ったノウハウを活かし様々な人の力を借りることで、大きな問題なく導入を進められました」。一連の動作すべてを自動化するのは初の試みだったが、工程内不良をなくし品質の均一化も実現できた。「本格的に量産するとなると現場の方が設備を操作することになるので、操作の簡略化や画面表示、音声案内などのインターフェイスも扱いやすいよう作業員の目線になって設定しています」。
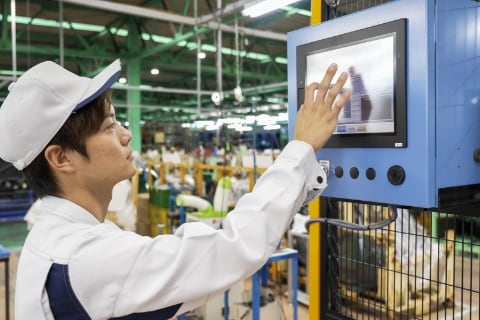

新しい製品づくりの流れが生まれる

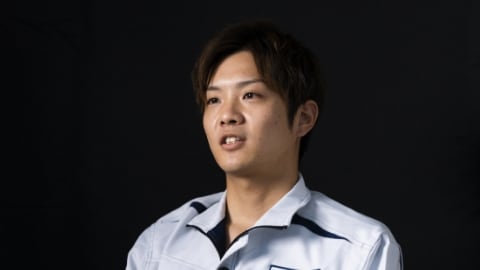
今回それぞれ所属の違う二人が声を揃えて助けられたというのが現場担当者の意見だった。「設計段階から現場の方にアドバイスをいただいたことで、過去車種に劣らない素晴らしい設計ができたと感じています。『CX-60』以降に計画されているすべての車種が全部門での意見交換会からスタートするようになり、弊社における製品開発のターニングポイントになったのではないでしょうか」。豊田の言葉に栗原も「現場担当者や先輩方をはじめとする仲間の協力あってこそのプロジェクトでした。様々な方と連携することでより良い製品づくりができました」と語った。モノづくりのプロたちが意見を出し合い妥協なく製品と向き合ったことで、新時代を牽引する『CX-60』にふさわしい自動車用ガラスが完成したのである。